Dynamic angle error compensation (DAEC™)
Find out more about dynamic error compensation.
Position sensing in high-speed applications
Propagation delay (also called output latency) is a feature of the position sensing circuit in a spinning motor. It is the time interval between the moment when the angle is measured by a position sensor, and the moment when the measurement signal is transmitted to the host microcontroller.
The propagation delay is problematic because it causes dynamic angle error at high rotational speed. This dynamic angle error increases with speed at a linear rate. Therefore the higher the propagation delay and the speed, the greater the dynamic angle error.
Electronically controlled motors, and brushless DC (BLDC) motors in particular, require extremely accurate data on the rotor's angle of rotation while turning at high speed.
The integrated dynamic angle error compensation (DAEC™) technology from ams OSRAM implements a compensation algorithm which almost completely eliminates the effect of the propagation delay inside the position sensor, yielding almost zero output latency. This technology enables the effective control of torque in BLDC motors and provides for highly efficient motor operation by eliminating vibration and other interfering mechanical effects.
Dynamic angle error compensation (DAEC™)
ams OSRAM position sensors with DAEC™ technology inside produce a smaller dynamic angle error, and are ideal for motor applications which operate at high rotational speed because of their ability to provide fast and accurate position measurements.
Because compensation is performed in the sensor itself, the user can implement a smaller and more cost effective design than a system which requires external compensation, for instance in a high-performance microcontroller. It also eliminates additional sources of system error such as sampling error.
Dynamic Angle Error Compensation (DAEC™) is a revolutionary new technology that yields almost zero output latency and ultra-fast refresh rates.
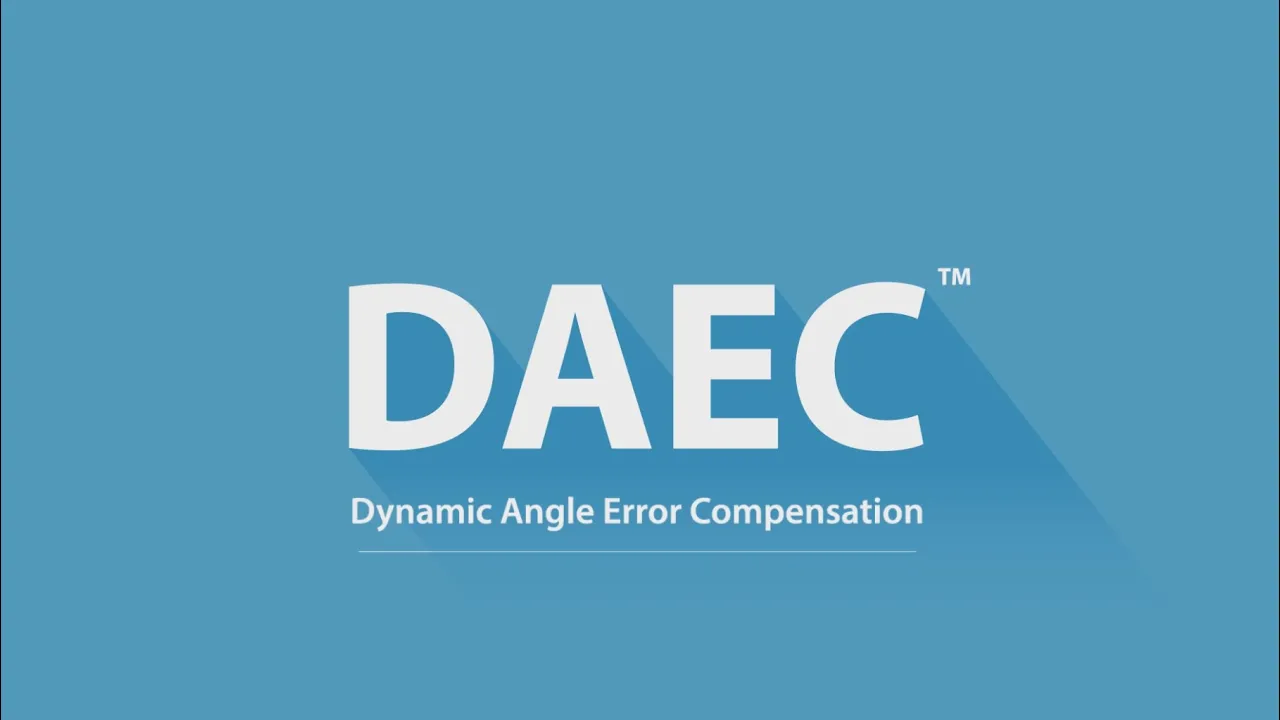